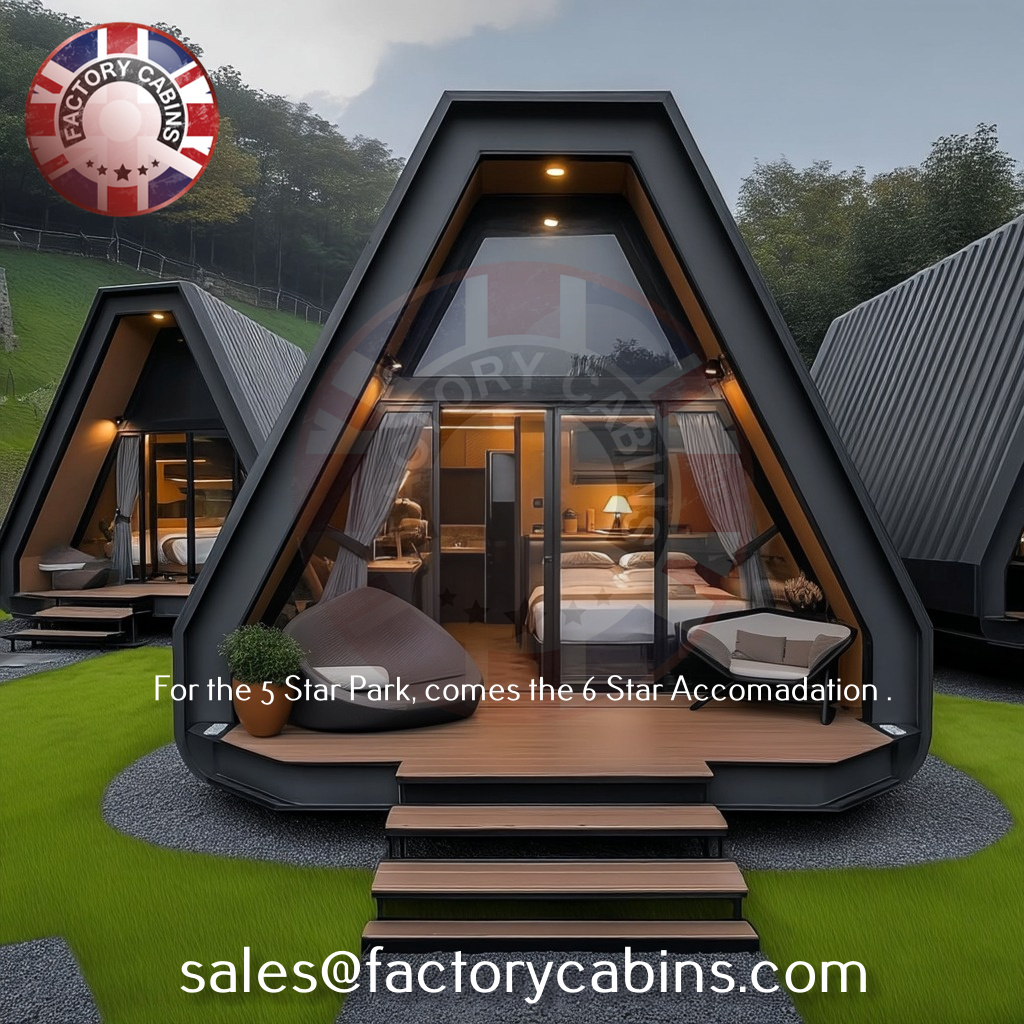
Think Outside the Box: Learn Why Our Revolutionary Camping Pods Are the Ultimate Investment in Your Park and the Future Your Visitors Crave.
Look around. Scattered across our lovely English countryside, there they are: bargain-basement camping pods. Boxlike wooden sheds, already appearing aged in some instances, ready to be the eyesores – and money pits – of the future. They’re an opportunity squandered.
A sunk cost that moulders in front of your eyes, bringing down your park’s attractiveness and your possible returns.
Of course, some firms provide superior pods, but their shapes are impractical, their designs uninspired, and their prices grossly out of proportion to the service provided.
This is when the future takes shape. Our second-generation camping pods aren’t an upgrade; they’re a total reimagining of what holiday accommodation is—and should be. We didn’t only design new pods; we designed a solution for park owners who desire more.
1. Breaking the “Cheap & Cheerful” Look (Because Cheep’s Not Cheerful for Long): Gone are the days of boxy, utilitarian eyesores. Our pods now boast sleek, contemporary lines and a thoughtfully integrated design. Picture structures that enhance the natural beauty of your park rather than clash with it. With their curved rooflines, superior cladding options that transcend basic treated timber, expansive glazing that frames breath taking views, and elegant finishes, these designs evoke an immediate sense of quality and desirability.
These pods are like high-end retreats, giving your park an instant reputation boost and attracting visitors willing to invest in a truly special experience. First impressions last – ours radiate comfort, sophistication, and value.
2. Made for Generations, Not Seasons (Your Investment, Secured) :>
The horror tale of pods rotting within 5 years concludes here. Longevity is key. We use advanced, engineered materials and construction methods created for contemporary architectural specifications. Consider higher, sustainably sourced timber composites, the latest weather-resistant membranes, and corrosion-resistant fixings. This is not merely wood; it is a system built to endure decades of British weather without ongoing, expensive maintenance.
Say goodbye to the repair, replacement, and lost revenue cycle.
Our pods are a genuine long-term investment, securing your capital and providing consistent returns year after year.
3. The Net Zero Advantage: Reducing Costs, Enhancing Attractiveness:
Sustainability is not a buzzword; it’s your next big profit centre. Our pods are designed from the ground up as Net Zero ambassadors:
Unparalleled Insulation: The high-quality thermal envelopes minimize heat loss,
If you look at the inside of the entrance you will see clearly what happens to pods only after 4-6 years, Rot!
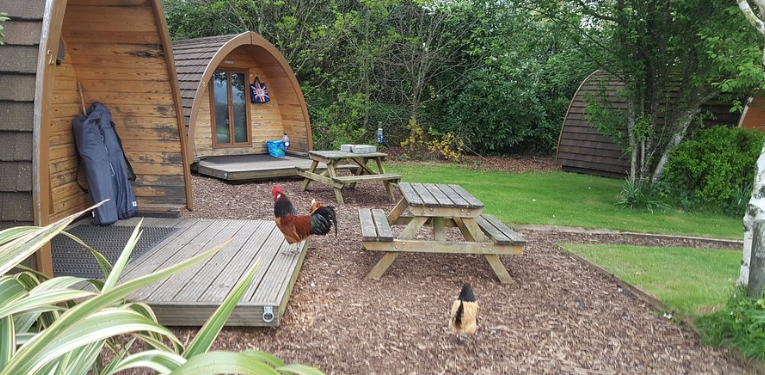
so that only a minimal amount of energy is needed to heat and cosy up guests, even in the winter months. Farewell to those sky-high heating bills.
Integrated Renewable Potential: Engineered to integrate readily with solar PV and other renewables, for on-site power generation that lowers not only operating costs but also your carbon footprint.
Energy-Efficient Design: Careful window location boosts passive solar heat during winter, and in summer, natural ventilation, thereby eliminating the necessity for artificial heating and cooling.
This directly impacts your bottom line: it results in significantly lower utility costs per pod and provides a compelling marketing message that attracts the increasingly eco-conscious traveller.
4. Park Owner Sanity (Low Maintenance, High Uptime) Designed For:
We understand your time is money. Instead of retro-type pods that require frequent staining, sealing, and patching, our designs emphasize low-maintenance durability. Timeless high-performance materials withstand fading, warping, and rot. Intelligently designed details minimize dirt traps and simplify cleaning. This means more time on guest experience and park management, less time and money on maintenance. Book more of your rental calendar and less of your headaches.
5. The ROI Revolution: Where Quality Meets Measured Returns: Yes, our pods are a more premium investment than the cheap ones that are everywhere. But this is where vision comes into play:
Longer Lifespan: A 20+-year pod versus one that’s deteriorating in 5 years completely alters the depreciation curve and long-term ROI.
Increased rental premiums are the result of better design, comfort, and green credentials that collectively achieve premium nightly rates and attract visitors year-round.
Substantially Reduced Operating Expenses: Cut down heating/electricity bills and low maintenance costs greatly increase net profit per pod.
Enhanced Park Reputation & Occupancy: Establish a reputation for sustainability and quality, drawing in more bookings and encouraging repeat guests.
Future-Proofed Investment: With building codes and guest expectations quickly evolving towards energy efficiency, our Net Zero-ready pods put you in front of this shifting curve.
Buying cheap pods is a false economy. When you buy our state-of-the-art camping pods, holiday accommodation, and glamping pods, you’re investing in the strong, lucrative, and popular future of your park. Say goodbye to eyesores and money pits.
Say goodbye to paying too much for unrealistic “premium” designs. Enter the future of camping accommodation. Are you prepared to turn your park into a shining example of excellence, comfort, sustainability, and high returns?
Give us a call today. Let’s discuss how our revolutionary camping pods can be your greatest asset. Camping Pods, Glamping Pods, and Holiday Units are revolutionizing the future of camping.
Invest for the long haul. Invest for the payoff.
Please call us on +44 208 226 1564
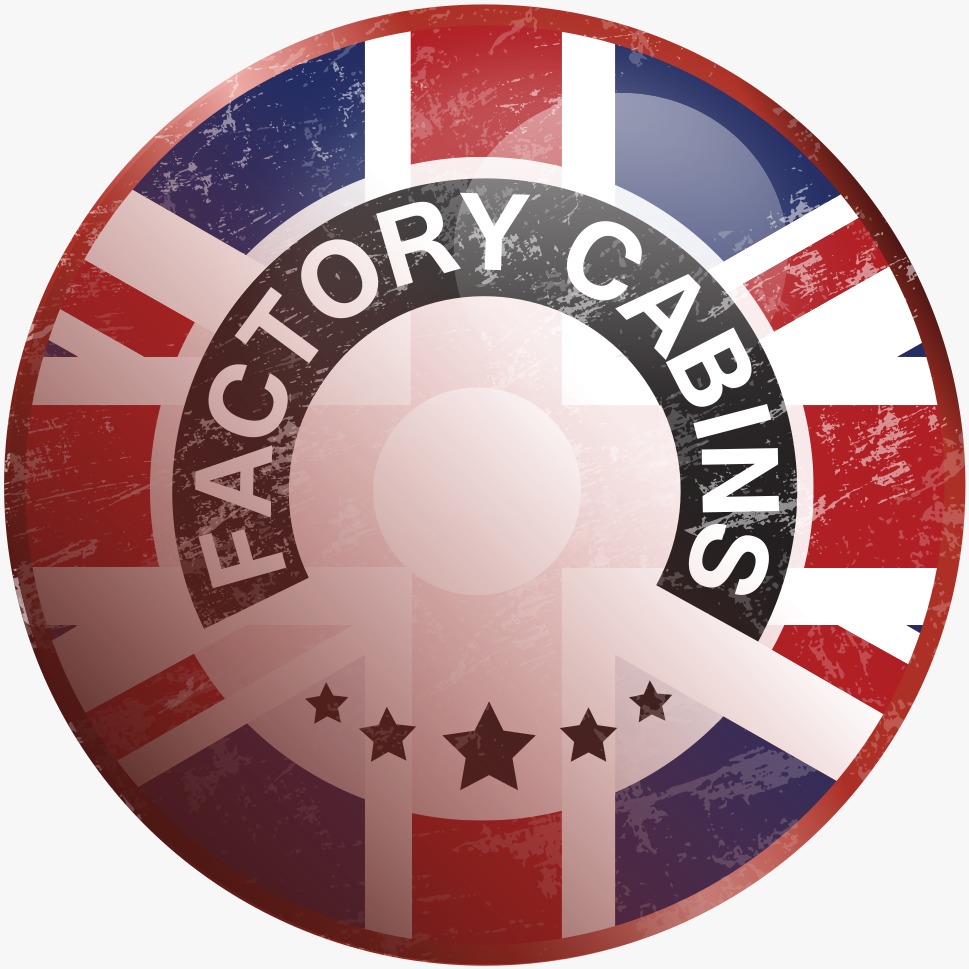