The BS 3632 Betrayal: Why Most Park Homes Are Built to Fail & How Factory Cabins LTD Constructs Legacy Investments That Defy Obsolescence
The dream is straightforward: a lovely, serene, and high-quality residential park home. A home of your own that is made for comfort, constructed to endure, and is a wise investment for the future. You search eagerly for the BS 3632 stamp – the British Standard for residential park homes – hoping that it will stand for quality and durability. You sign on the dotted line, thinking you’ve made an excellent decision.
Then reality bites. Hard.
Within years, sometimes just months, you start to hear rumours of “new regulations,” “future insulation standards,” “compulsory design revisions.” Your brand-new park home, allegedly constructed to the latest BS 3632, all of a sudden seems compromised, possibly non-compliant in the not-so-distant future, and most importantly, valued at a lot less than you purchased it for. Why? Due to the fact that the ugly reality is this: a lot of the park home industry is established on a basis of planned obsolescence and borderline deceit.
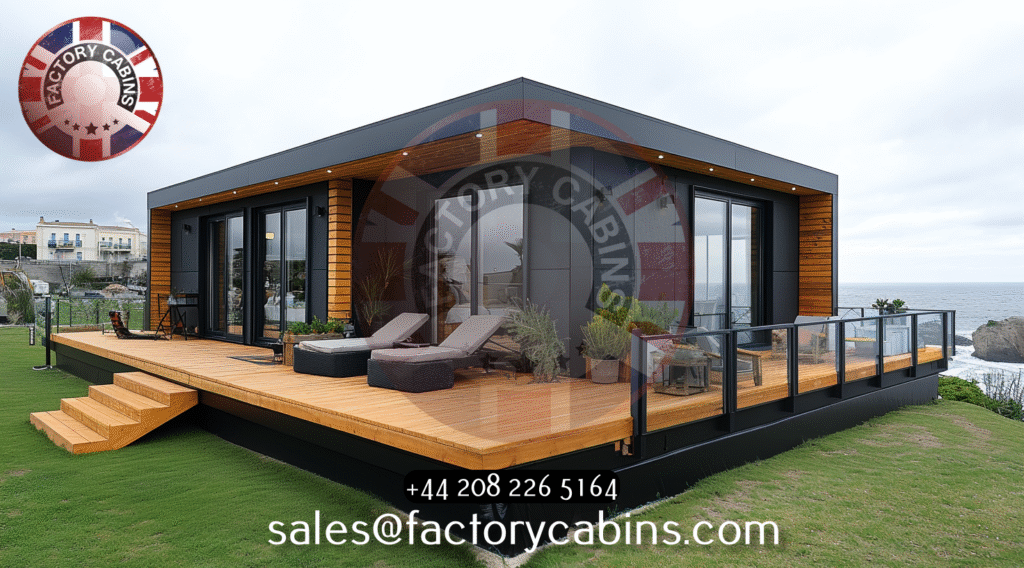
It’s a sector full of players who see the BS 3632 not as a mark of excellence, but as a minimum requirement to just get over. They construct to the standard, not above it. They utilize materials and designs engineered to pass today’s tests with the least expense, with no thought for tomorrow’s unavoidable tightening of standards. They are, in effect, waiting for the government to inform them what not to construct next year, making your present investment outdated. It’s a cycle of built-in depreciation, an intentional robbery of your hard-earned capital the instant you invest.
The BS 3632 Loophole: Designed for Obsolescence, Not Legacy.
Today’s BS 3632 standard is a critical minimum, providing essential safety, structural integrity, and basic thermal performance for park homes in the UK. But it is just that – a minimum. As with all building standards, it moves on. Climate change pressure, technological innovation, and a better grasp of energy efficiency and occupant health continually push revisions.
The industry’s dirty secret? Many manufacturers see these inevitable updates not as a challenge to innovate, but as a business model. Here’s how the betrayal works:
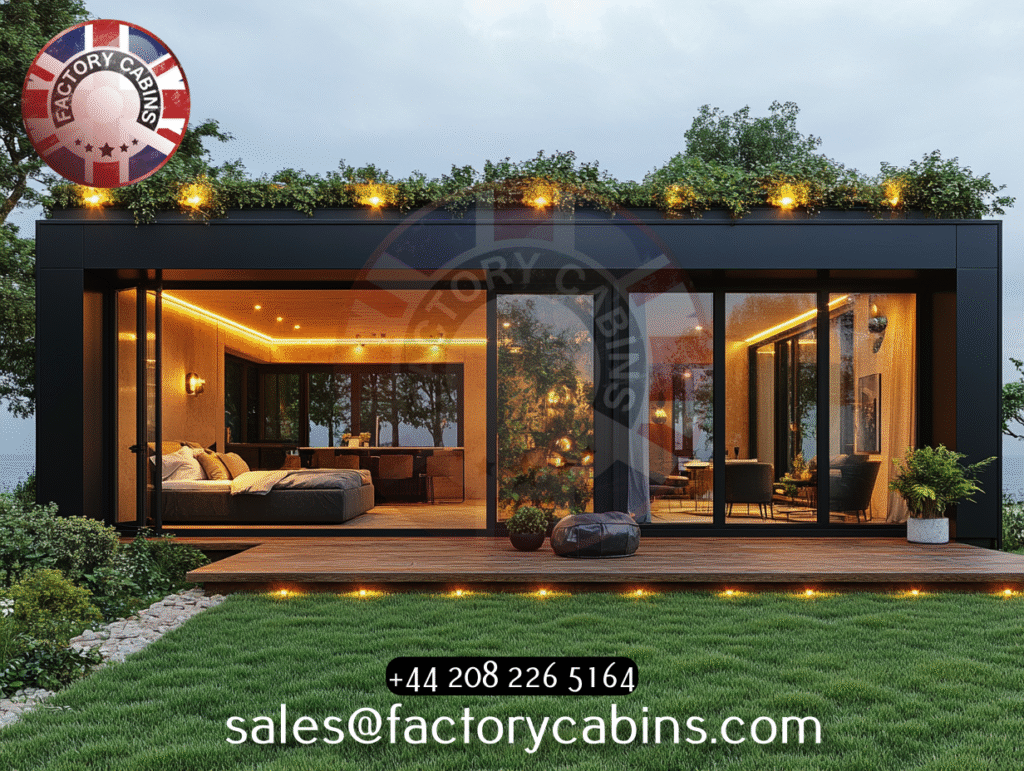
1. Bare Minimum Build: Park Homes are built to specifications and materials that barely comply with the minimum BS 3632 standards. Insulation is at the minimum acceptable level; heating systems are rudimentary; glazing is standard double rather than enhanced triple; air tightness is acceptable, not outstanding.
2. Zero Futureproofing: No investment is made in technologies or designs that pre-empt future legislation. Why pay extra now when the government will make everyone do it later (so they can bill you again)?
3. The Depreciation Trap: The moment a new standard is suggested or implemented (e.g., increased U-values for insulation, obligatory renewable energy integration, more demanding air permeability goals), houses constructed merely to the earlier standard instantly lose considerable value, up to 90%. They are viewed as outdated, inefficient, costlier to operate, and less easy to sell or finance. The depreciation is intentionally created by short-sightedness on the part of the manufacturer.
4. The “Snake Oil” Sales Pitch: Purchasers are usually sold on price and aesthetics, with the BS 3632 compliance being presented as a comforting badge, hiding the reality that the house is constructed to a standard already on the way to obsolescence. Claims of “quality” are hollow when the underlying agenda guarantees speedy devaluation.
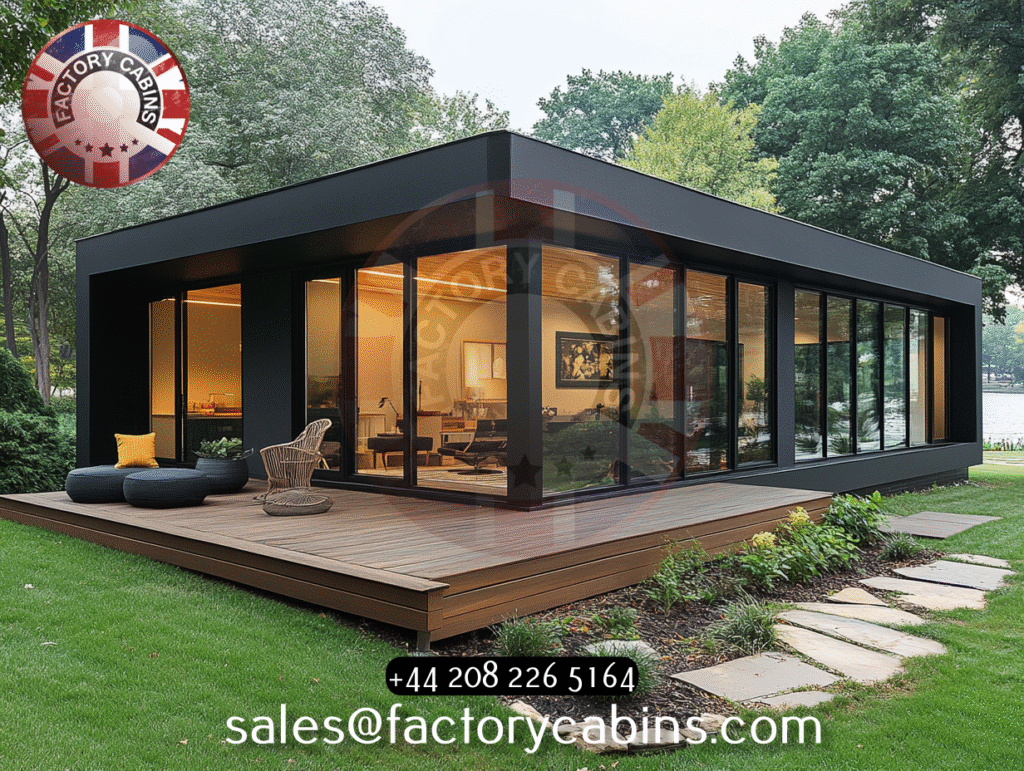
5. Mother Nature? An Afterthought: Most standard BS 3632 houses, while satisfying basic structural loads, are not well prepared to actually exist and survive in the face of more extreme weather – protracted heatwaves, violent storms, driving rain, or harsh cold snaps. Resilience is traded for affordability.
The outcome? You, the purchaser, are left with a park Home that quickly loses value, potentially expensive retrofits to comply with new codes, and that might not provide the long-term comfort, efficiency, or durability you anticipated. Your investment loses value from day one. This is the theft.
Factory Cabins LTD: Shattering the Cycle, Building BS 3632 Legacy Homes
At Factory Cabins LTD, we saw this systemic breakdown and said no. We posed a basic question: Why can’t a park home be a true, appreciating asset? Why can’t it be constructed not only for compliance today, but for leadership tomorrow? Why can’t it be a fortress against the elements and a bastion of efficiency for generations?
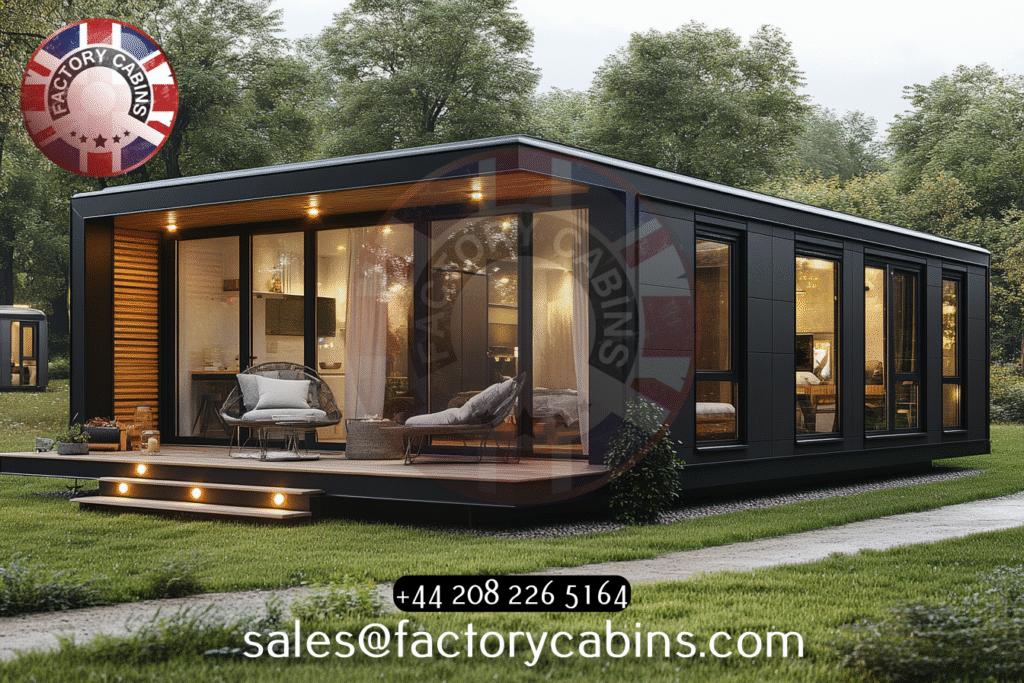
The response is: It can. And that is precisely what we construct. Our BS 3632 Residential Park Homes are not merely compliant; they are the antithesis of the industry norm.
1. Surpassing Standards Today, Defying Obsolescence Tomorrow:
We don’t construct to the minimum BS 3632; we construct above it, foreseeing and incorporating the technologies that will be required in 2030, 2050, and beyond. Your Factory Cabins Park Home isn’t awaiting an update to a government specification; it’s already there.
Thermal Performance: Gone are the minimum U-values.
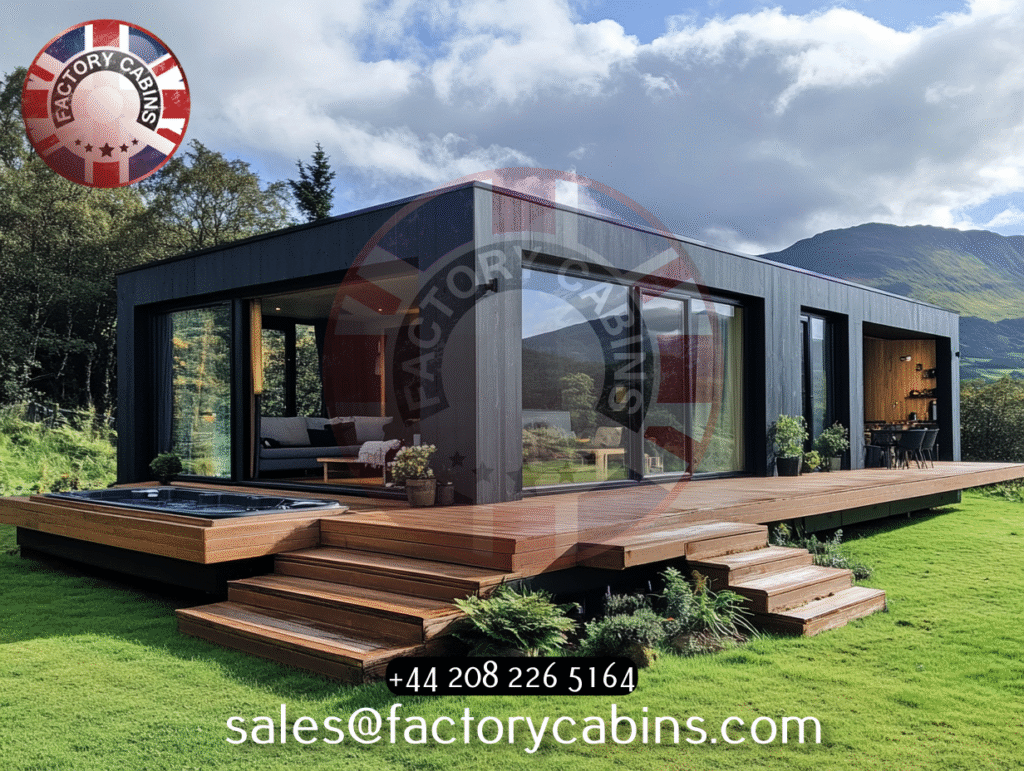
Our Park Homes has advanced structural frames with ultra-low thermal bridging, next to none, combined with substantially higher levels of insulation (typically 50%-60%+ above current standards) in walls, floors, and roofs. We use the latest materials such high-performance mineral wool systems. This is not merely a matter of comfort; it’s about keeping your home’s energy efficiency well ahead of the game long after standards tighten, safeguarding its value and your ongoing costs.
Air Tightness: We attain exceptional air permeability rates (that shatter the BS 3632 requirements) through careful design, accurate manufacture, and sophisticated sealing systems. This is not only important for heat retention but also for moisture management and indoor air quality – aspects under growing scrutiny in future regulations.
Glazing: Triple-glazed units with low-emissivity coatings and argon fills are the norm, not a costly upgrade. This offers better thermal and acoustic performance, futureproofing against energy and noise standards.
Smart Systems Integration: Our homes are pre-wired and structurally prepared for the easy integration of tomorrow’s smart home systems, renewable energy technologies (solar PV, battery storage), and ultra-efficient heating/cooling options such as advanced air-ground source heat pumps. We don’t simply leave a space; we create the pathway.
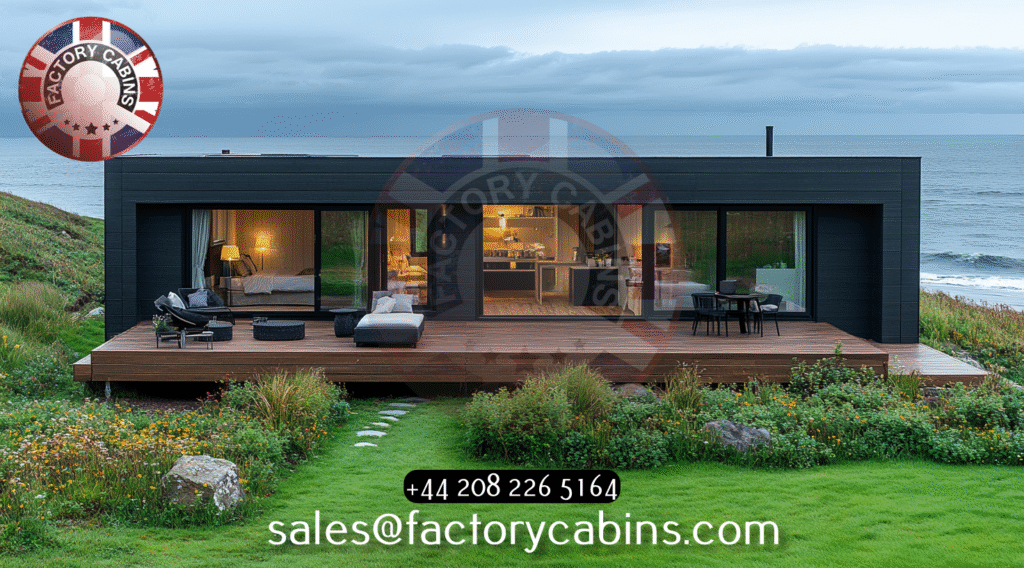
2. Net Zero Ready: Where the Government Fails, We Deliver
The difficulties of the UK government to retrofit current housing stock to net zero are well documented. It’s complicated, disruptive, and costly. We address this issue at source. All Factory Cabins BS 3632 houses are designed as a Net Zero Ready Platform.
Inherent Efficiency: Super-insulated, ultra-airtight envelope radically lessens the need for energy in the first instance. This is the foundation of true net zero.
Renewable Foundation: Building structure and electrical systems are designed for optimal integration of enough roof-mounted solar PV and battery storage to provide a large fraction, or even all, of the remaining energy need. We quantify this potential at design time.
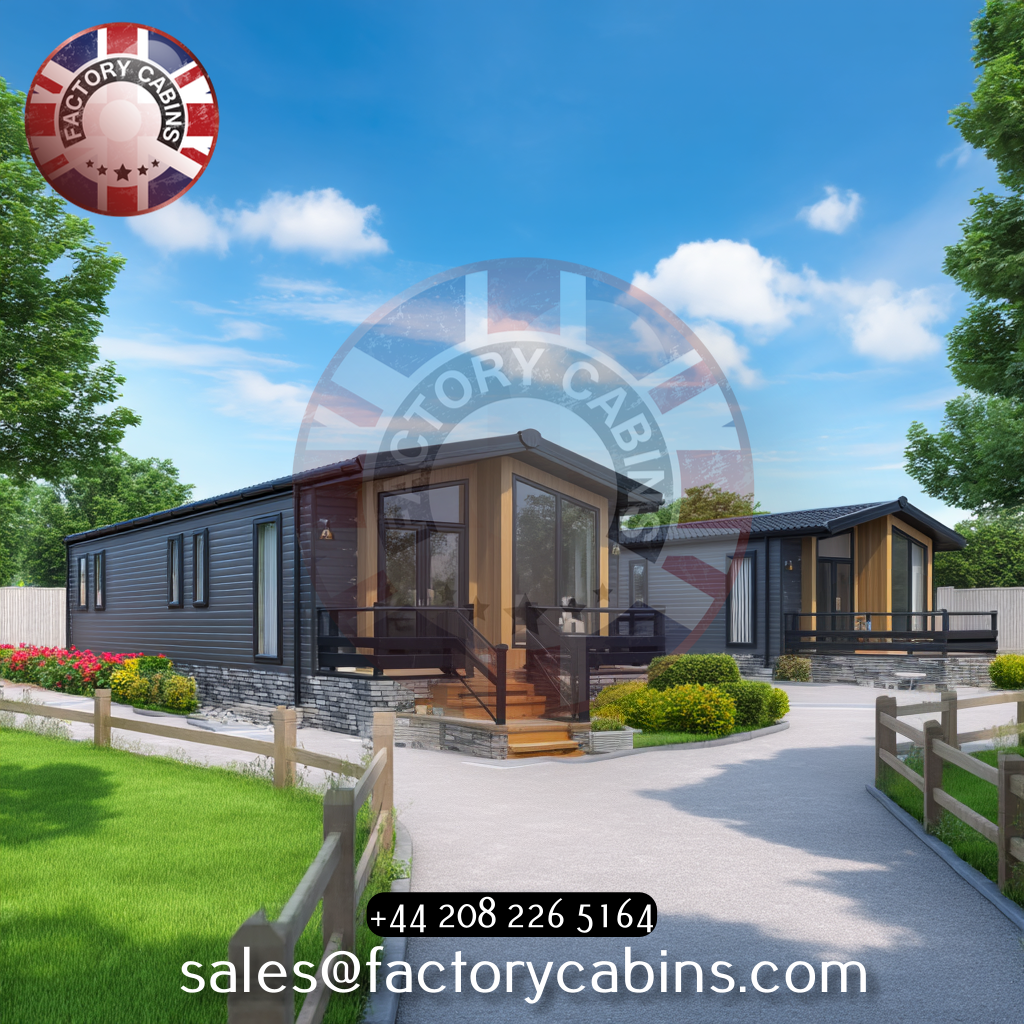
Low Carbon Heating: Compatibility with the newest high-efficiency, low-carbon heating technologies (such as next-generation heat pumps) is designed in.
Future Fuel Independence: By drastically reducing demand and facilitating renewable generation, your home is shielded from volatile fossil fuel prices and positioned perfectly for the inevitable full transition to a renewable grid.
Where others wait to be compelled, we create the solution now. Your house is not a part of the climate issue; it is an integral part of the solution, making it more attractive and valuable as net zero goals become mandatory.
3. Engineered Appreciation: Your Home as a Growing Asset
By constructing years ahead of the present standards and incorporating future-proof technologies: Demand Outstrips Supply: As codes tighten, existing homes (constructed to the bare minimum) quickly lose value and attractiveness. Homes like ours, already surpassing future requirements, grow rare and more desirable.
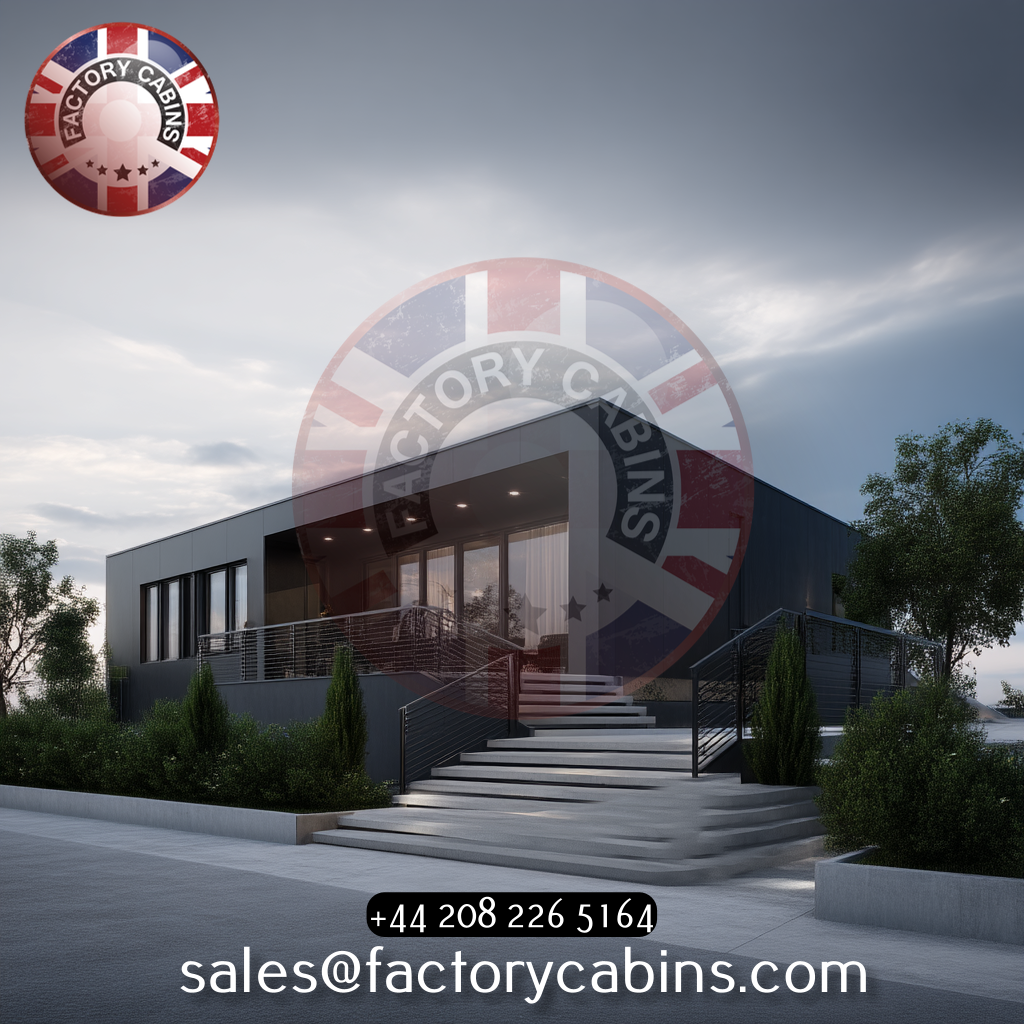
Buyers pursue them to escape the expense of retrofits and lofty energy bills.
Lower Lifetime Costs: Substantially lower energy bills and little need for future upgrades mean big long-term savings, which make your home less expensive to live in and more appealing to future buyers. Superior Quality Perception: The visible application of high-tech materials, better construction methods, and included technology provides a physical impression of greater quality and durability, warranting a higher price.
Resilience Premium: In a time of climate uncertainty, a dwelling that is proven to resist extremes is a prized refuge, once again enhancing desirability.
We don’t merely arrest depreciation; we create the conditions for true appreciation. Your Factory Cabins home is a legacy asset.
4. Designed to Withstand Mother Nature & the Test of Time:
BS 3632 specifies structural loads. We design to surpass them, with resilience engineering:
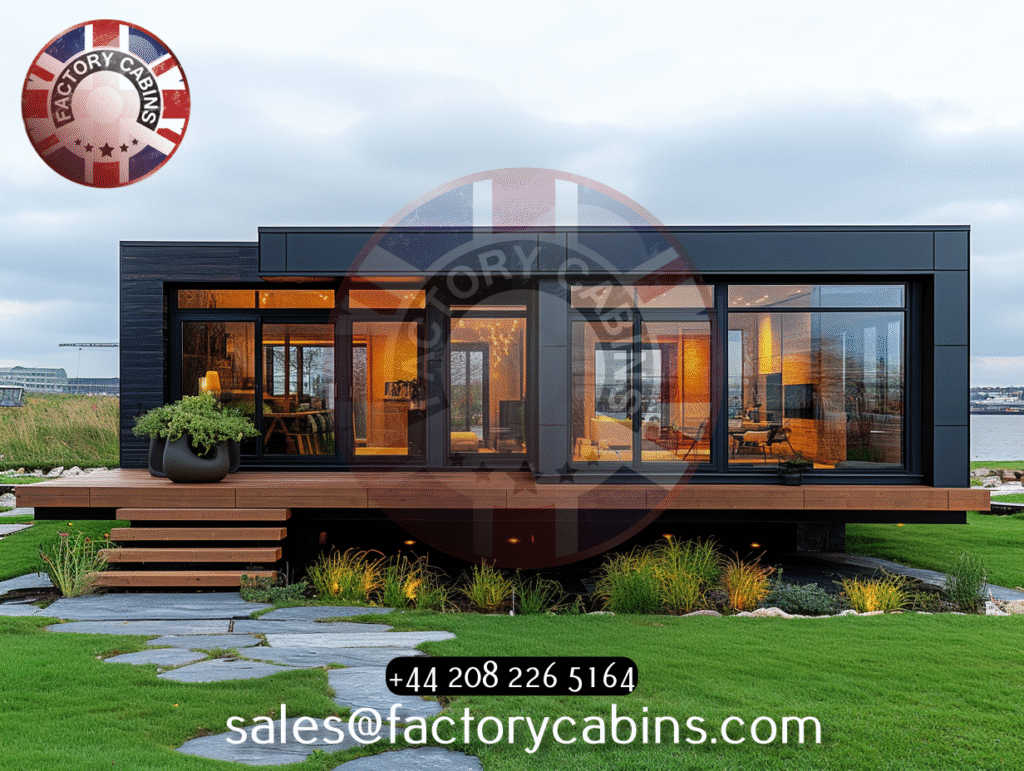
Improved Structural Integrity: Strong framing systems, detailed connections, and material selection strategies provide enhanced performance in high wind loads, snow loads, and soil movement.
Weatherproofing Fortress: In addition to minimum requirements, we use high-performance breathable membranes, enhanced cladding systems, and careful detailing around windows, doors, and roof edges to provide a watertight barrier to driving rain, humidity, and extreme temperature variations.
Durable Materials: We specify materials not just for initial cost, but for proven long-term performance and resistance to weathering, UV degradation, and wear. This includes high-performance composites, treated timbers, and premium finishes.
Precision Manufacturing: Constructed in our factory environment, which is controlled to minimize errors, each component is cut, assembled, and sealed to millimetre precision, removing the weaknesses and irregularities present in conventional on-site construction. Quality control is strict and continuous.
Your house is not merely “compliant”; it’s a lasting refuge built to safeguard you and your investment for generations.
Stop the Theft. Invest in Legacy. The decision is clear. You can play the industry’s rigged game: purchase a home designed to fail, see its value collapse as codes evolve, endure increasing bills, costly upgrades, and the pain of betrayal. Or you can end the cycle with Factory Cabins LTD.
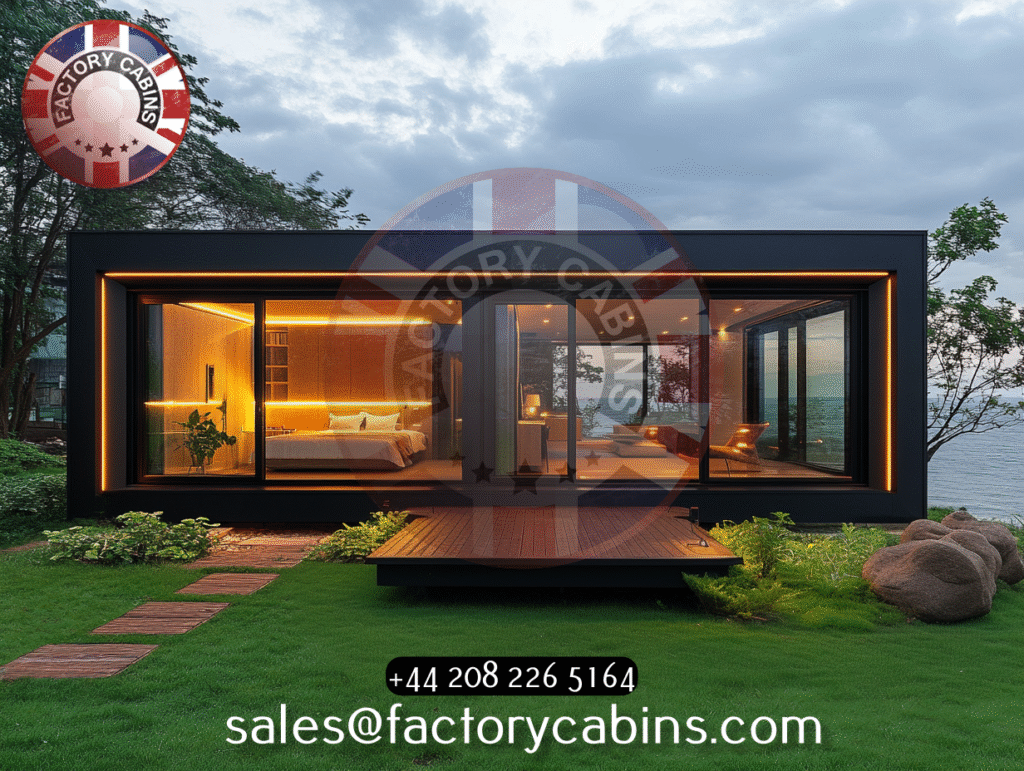
We won’t construct obsolescence. We construct BS 3632 Legacy Homes: Future-proofed strongholds of efficiency, engineered for appreciation, with net zero performance today, and built to remain unshakeable in the face of whatever Mother Nature and the years bring.
Don’t buy just a park home. Buy a legacy. Insist on the specification that safeguards your future: The Factory Cabins LTD BS 3632 own Standard. It’s more than a home; it’s a statement that you won’t be a victim of an industry constructed on deliberate failure.
Let’s create something that really endures, and really grows. Contact Factory Cabins LTD today. Feel the difference that real foresight, uncompromising quality, and honest engineering makes.
Become the owner of a home that defies depreciation and shapes the future.
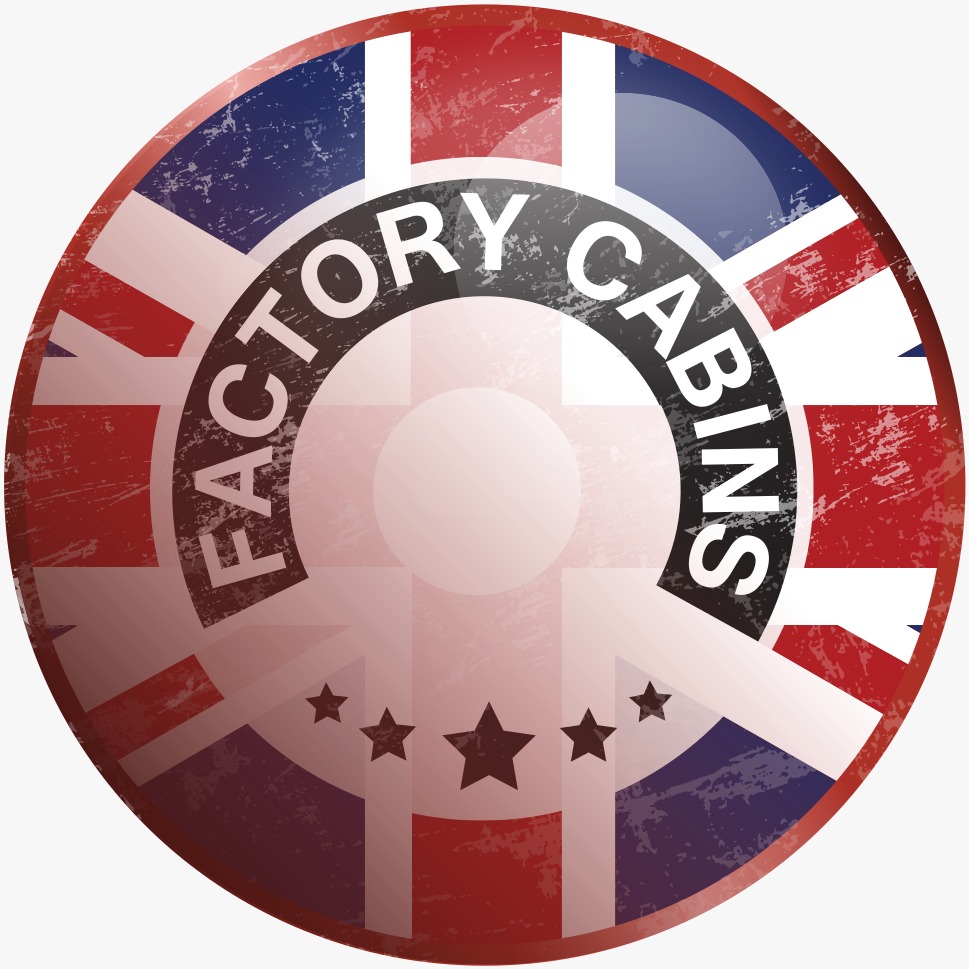